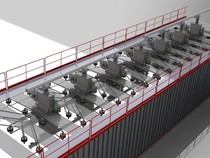
E’ il più sofisticato sistema di combustione di prodotti solidi per l’industria dei laterizi, esistente sul mercato mondiale. E’ l’unico impianto che non solo si avvicina ai più avanzati sistemi di combustione a gas ma è l’unico sistema che riesce a dare una regolazione perfetta nella zona servita da ogni bruciatore e oltre ad una regolazione perfetta del rapporto carbone/aria relativamente ad ogni canna di alimentazione, riesce a dare una regolazione perfetta della quantità della miscela carbone-aria relativamente ad ogni canna di alimentazione.
Nessun altro sistema riesce infatti a definire e controllare il livello di granulometria del combustibile solido (è noto come una minore granulometria garantisca una migliore combustione immediata), la temperatura all’interno del forno relativamente ad ogni bruciatore, la portata della miscela aria/carbone relativamente ad ogni canna di alimentazione, il rapporto carbone/aria relativamente ad ogni canna di alimentazione. L’impianto consta di due gruppi di macchine:
-
Gruppo macinazione a granulometria controllata ed insilamento
- Gruppo di combustione sul forno ( CARBOJET, TURBOJET )
“ Il SBAS (SOLID BURNING ALPINA SYSTEM) è l’unico sistema che consente nell’insieme:
-
Definizione e controllo perfetto della granulometria impostata del Polverino di Pet Coke
- Deposito settimanale del polverino di Pet Coke
- Controllo della temperatura relativamente ad ogni bruciatore
- Controllo e regolazione dell’aria di trasporto e di combustione
- Regolazione perfetta per ogni canna di alimentazione del rapporto combustibile/aria
- Regolazione perfetta per ogni canna della portata della miscela Combustibile/aria
I DUE TIPI DI IMPIANTO
L’impianto nelle versioni Carbojet System e Electrojet System, prevede un gruppo di macinazione ed insilaggio del carbone ovvero del Pet Coke, un sistema di trasporto a coclee del prodotto micronizzato, un sistema di insilaggio del polverino, infine l’impianto di combustione vero e proprio costituito da una serie di bruciatori a controllo elettronico.
La configurazione speciale del sistema di macinazione, con l’impiego di uno speciale separatore statico o dinamico a seconda delle esigenze, di un filtro a maniche e del ventilatore di estrazione dell’aria di trasporto del polverino attraverso il filtro, consente un dosaggio perfetto del range di granulometria. Un inverter di gestione della rotazione del ventilatore infatti garantisce una variazione della depressione lungo il separatore con conseguente variazione della granulometria, così da adattarla alle esigenze della combustione.
Il trasporto del polverino, dal serbatoio di raccolta al di sotto del filtro, mediante coclee di tipo meccanico elimina qualsiasi fuoriuscita di polvere di carbone nell’ambiente esterno essendo il sistema operante a pressione ambientale.
L’impianto di combustione vero e proprio costituito da una serie di bruciatori del tipo Carbojet o Electrojet, garantisce una perfetta combustione con un controllo zona per zona della miscela aria/carbone e un controllo locale delle temperature all’interno del forno, mediante l’impiego di termocoppie al servizio di ciascun bruciatore.
Anche se non indispensabile, è utile l’installazione nelle prime quattro file di bocchette di alimentazione sulla volta del forno, di due gruppi a gassificazione a olio pesante, ovvero ad autoaccensione a gas.
Il pet coke viene prelevato dal deposito al coperto mediante l’impiego di una pala caricatrice che provvede a caricare un cassone di alimentazione a tre coclee, di conformazione speciale per il convogliamento del combustibile verso il sistema di macinazione vero e proprio.
Il cassone di alimentazione è infatti dotato di tramogge a parete verticale e tre coclee di estrazione alla base, per lo scarico del Pet Coke. Il profilo della tramoggia a parete verticale e l’insieme delle tre coclee alla base sono studiati per evitare qualsiasi ponte possa formarsi sulla massa del combustibile solido.
Il Pet coke viene convogliato verso un sistema di trasferimento del tipo a coclea ovvero a tappeto in gomma. In caso di distanze notevoli possono infatti essere utilizzati sistemi di trasporto a coclea altrimenti possono essere utilizzati nastri in gomma. Un sistema di rilevazione metalli è inserito sopra il nastro di trasporto così da evitare il convogliamento accidentale di metalli verso il mulino a martelli.
Il Coke sarà scaricato dal nastro trasportatore nel dosatore che ha il compito fondamentale di assicurare una alimentazione regolare e uniforme al mulino tramite la grossa coclea alla base del dosatore stesso. Il dosatore, equipaggiato con misuratori di livello, riceve il Coke dal nastro di alimentazione ovvero da una coclea per il suo convogliamento appunto verso il mulino tramite una valvola stellare.
Il mulino riceve il combustibile in pezzatura variabile non superiore di norma a 25 mm con umidità inferiore al 10%, miscelato al residuo di ritorno dopo la macinazione ( la cui granulometria è superiore alla dimensione massima fissata ) assieme ad un flusso d’aria calda che sarà il veicolo di trasporto successivo del polverino all’uscita dal mulino.
La macchina è disegnata in modo da ricevere aria calda dal recupero del forno o da altra sorgente sussidiaria; l’aria ha il duplice compito di eliminare possibili incrostazioni di Coke sulle pareti della macchina stessa a causa dell’umidità del Coke stesso in modo che il mulino possa lavorare correttamente alla sua piena efficienza e di trasportare il polverino di Coke versoi il separatore statico ed infine verso il filtro a maniche. L’ingresso dell’aria ed il suo flusso verso il filtro a maniche è garantito da un ventilatore ad alta prevalenza posto oltre il filtro stesso.
Il mulino del tipo a martelli, è dotato di un rotore centrale sul quale sono appunto fissati I martelli oscillanti su perni, e di una carcassa dentellata sulla quale avviene l’impatto del materiale solido. Nella parte superiore una apertura consente la fuoriuscita per depressione, del polverino verso il separatore.
Il movimento del carbone dopo il mulino è garantito da un flusso d’aria prodotto dal ventilatore ad alta pressione dopo il filtro. Durante il suo trasporto il polverino di carbone completamente essiccato viene convogliato nel separatore in cui avviene la separazione della parte fine dalla grossolana che ritorna in ciclo e quindi fermato dal filtro precipita nella parte inferiore del filtro stesso dove attraverso una valvola stellare viene convogliato verso la coclea e l’elevatore a tazze che lo porteranno nel silo.
La maggiore o minore apertura delle alette del separatore, così come una variazione della depressione nel separatore, consentono un dosaggio perfetto del range di granulometria richiesto in funzione del tipo di combustibile solido impiegato
Un elevatore a tazze trasporta il polverino di pet coke verso due depositi di capacità equivalente a 5 giorni di riserva.Il filtro lavora “in depressione”; l’aria polverosa viene aspirata dal ventilatore centrifugo, posto a valle del sistema, il quale crea la necessaria depressione per vincere sia le perdite di carico del circuito, sia quelle provocate dalla resistenza dei filtri, una volta giunti a regime.
Il filtro necessita di qualche giorno per giungere a regime per dare la massima efficienza dopo che si é formato, sul mezzo filtrante, un limitato accumulo di polvere (cake) che opera da prefiltro. Perciò non é opportuno procedere a rilevazioni strumentali della polverosità residua, al camino, subito dopo la messa in esercizio. L’aria polverosa, aspirata dal ventilatore, entra nella camera di decantazione ove avviene, per gravità, un rallentamento della velocità di ingresso ed una prima separazione tra le particelle più grossolane e quelle più fini.
Le maniche sono disposte verticalmente nella camera filtrante e vengono attraversate dall’aria dall’esterno verso l’interno. L’aria perde il contenuto di polveri che si depositano sulla superficie esterna delle maniche filtranti. L’aria, nel suo percorso, giunge nella “camera pulita” attraverso il foro entro il quale é collocato l’eiettore tipo venturi. Da qui l’aria filtrata esce dal corpo del filtro, attraversa il ventilatore e viene espulsa, in atmosfera attraverso il camino.
Il sistema di pulizia “reverse pulse jet” avviene in controcorrente per mezzo di getti di aria compressa soffiata all’interno delle maniche, fila dopo fila, in ciclo, secondo il programma impostato sul sequenziatore elettronico in dotazione. L’aria compressa viene soffiata all’interno dell’eiettore venturi, di cui é corredata ogni manica. L’onda di pressione provocata dal breve, ma intenso, getto di aria compressa deforma meccanicamente la superficie della manica. L’onda d’urto provoca il distacco della polvere depositatasi sul lato esterno della cartuccia. Poiché la pulizia avviene durante il normale funzionamento del sistema di aspirazione, si verifica che parte della polvere staccatasi, grazie all’ “effetto venturi”, venga di nuovo richiamata sulla manica dal ventilatore. E’ necessario procedere alla “post pulizia” consentendo al sistema “reverse pulse jet” di continuare a lavorare, per un breve periodo, anche dopo l’arresto del ventilatore centrifugo. L’assenza di aspirazione facilita la pulizia delle maniche dalle quali la polvere si stacca pressoché totalmente per cadere in tramoggia. Il tempo necessario alla “post pulizia” é rapportato alla natura delle polveri, alla loro granulometria e concentrazione. Sofisticati sequenziatori elettronici presiedono alle operazioni di pulizia, durante e dopo il funzionamento dell’impianto di aspirazione, controllando: il valore di “Δp”, l’intervento programmato del sistema di pulizia e di “post pulizia” e il rivelatore di fughe di polvere: vengono infine segnalate anche eventuali fughe di polvere individuando la fila in cui si trova la manica fessurata.
Le polveri filtrate e separate dall’aria vengono raccolte in un apposito contenitore metallico posto alla base del sistema filtrante e veicolato all’esterno per mezzo di una valvola rotativa ovvero di una coclea.
Il polverino di carbone all’uscita dal contenitore metallico posto alla base del filtro viene convogliato verso un elevatore a tazze a tenuta stagna che provvede al trasporto del polverino verso il silo di deposito. Come si nota dunque l’unico trasporto pneumatico del polverino in tutto l’impianto, avviene dal mulino verso il filtro. E tale trasporto avviene in depressione di conseguenza non vi è la minima dispersione di polvere all’esterno dei condotti.
A partire dal filtro il trasporto nel suo insieme avviene in modo meccanico con l’utilizzo di elevatori a tazze ovvero di coclee.
PERCHE’ PUNTARE SU UNA POLVERIZZAZIONE SPINTA E CONTROLLATA
Nel corso della combustione non tutta l’aria viene a contatto con la superficie del combustibile, quindi la combustione avviene in eccesso d’aria, cioè in presenza di una quantità di aria maggiore di quella stechiometricamente necessaria. Considerando che l’aria in eccesso assorbe parte del calore della combustione, si cerca di ridurre l’eccesso d’aria al minimo necessario, cioè si tenta di essere quanto più vicini possibile all’aria teorica.
Infatti utilizzando l’aria teorica si realizza la massima temperatura di combustione, quindi il massimo rendimentotermodinamico del ciclo termico.
L’aria teorica dipende dalla natura del combustibile relativo, ed è un limite inferiore teorico alla quantità d’aria effettivamente necessaria per la combustione completa, dato che l’efficienza non è generalmente pari al 100%.
L’eccesso d’aria di solito è nullo in presenza di combustibili gassosi, in cui il mescolamento fra l’aria ed il combustibile è a livello molecolare, mentre sale con combustibili liquidi nebulizzati o solidi polverizzati in modo molto fine, per arrivare a valori notevolmente elevati con combustibili solidi di grossa pezzatura. Questo spiega come la ricerca di una polverizzazione spinta e costante nel tempo dia garanzia di resa termica. Per poter accelerare la combustione si adopera una turbolenza, la quale aumenta il mescolamento tra combustibile e comburente, velocizzando la combustione.